贫铁矿(铁品位较低的铁矿石)

VLoG
次浏览
更新时间:2023-05-20
贫铁矿
铁品位较低的铁矿石
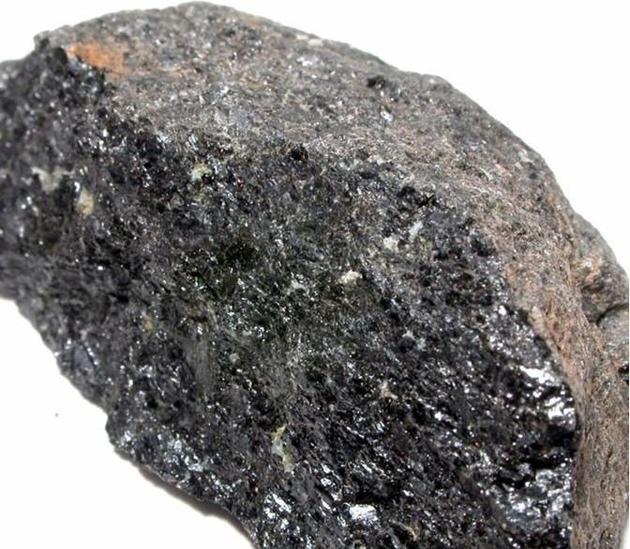
基本信息
中文名 | 贫铁矿 |
外文名 | Lean ore |
类别 | 冶金工程 |
运用领域 | 冶炼 |
材质 | 含铁30%~40% |
主要成分 | 铁,大量脉石 |
特点 | 渣量很大 |
收起
基本介绍
中国铁矿石资源丰而不富,在约500亿t储量中97.7%为贫矿,平均品位33%,低于世界铁矿石平均品位11个百分点,含铁量大于50%的富矿仅占2.3%,绝大部分须经选别方可入炉。中国铁矿石资源质量不高,其矿石大都以细粒条带状、鲕状及分散点状结构存在,甚至呈显微细粒结构。有些是多金属共生复合矿床,一些有价矿物往往需细磨至200目占90%才能单体分离,给选别等作业带来了难度。在开发过程中消耗大宗能量的同时,也给环境带来了污染。
我国铁矿石对国际市场的依赖程度已超过50%,且已成为我国钢铁工业经济安全的重大隐患。目前部分老矿山因开采多年资源接近枯竭或相继闭坑,因此超贫铁矿资源化利用已迫在眉睫,这对于挖掘我国铁矿资源的潜力,提高国内铁矿资源保障安全程度等均具有重要意义。
利用现状
我国95%以上的铁矿石储量为贫矿,平均品位仅32.00%左右。据国土资源部统计,截止2003年底,我国保有已探明的铁矿储量和资源量576.71亿t,其中表内矿(“经济储量”)166.86亿t,表外矿、超贫矿(“边际经济储量”、“次边际经济储量”)246.83亿t,其中磁铁矿矿石占48.8%,钒钛磁铁矿矿石占20.8%,赤铁矿矿石占20.8%,菱铁矿矿石占3.7%,褐铁矿矿石占2.4%,共生矿占3.5%。
由于受当时技术水平和经济效益的制约,一方面大多数现有铁矿山在开采过程中剥离出的大量超贫表外矿和贫杂矿矿石被堆置而未利用,另一方面还有大量超贫铁矿石至今尚未开发利用。例如马钢南山矿区低品位磁铁矿矿石累计探明资源量6.12亿t,平均含铁品位21.72%;攀枝花矿区含铁品位在15.00%~23.00%的超贫(含表外)钒钛磁铁矿矿石其储量近2.5亿t。另外据不完全统计,华北地区尚有数十亿t未开发利用的超贫磁铁矿矿石或表外磁铁矿石,鞍山地区尚有数亿t未开发利用的超贫赤铁矿矿石或表外赤铁矿矿石。低品位铁矿石的利用存在以下几方面技术难题。
(2)采矿过程中,矿石损失率和废石混入率难以控制,导致入选矿石的品位难以控制。另外表外矿资源量大,矿山企业在开采过程中,若废弃表外矿,需占用排土场,影响环保;若回收表外矿,降低了采出矿石品位,大大影响选矿精矿品位和金属回收率。
(3)由于矿石的铁品位低、相对难磨难选、选矿比大,若采用常规的选矿技术处理,将造成精矿成本高、矿山经济效益差或亏损。如高村铁矿出矿品位19.47%,选矿比4.50,与全国重点铁矿山相比,品位低11个百分点,选矿比高2.0,每吨精矿的选矿成本增加150元左右。
(4)由于受干式磁选设备分选原理的限制,矿石在较细的粒度下采用干式磁选抛尾效果很差,而目前尚未有成熟的适合细碎产品抛尾的高效湿式磁选设备。
根据资料报道,国外工业发达国家几乎未开发利用超贫、表外铁矿石,只有个别国家已开发利用超贫、表外磁铁矿矿石。比较典型的实例是前苏联卡奇卡纳尔采选公司选矿厂,所处理的矿石为铁品位15.8%的钛磁铁矿矿石,年处理量4000万t,精矿品位为61.50%左右,选矿比接近6。该选矿厂还从选铁尾矿中综合回收钛铁矿、硫化矿,同时提取辉石、斜长石用于制取建筑材料。
技术现状
资源高效利用的途径之一就是降低采出矿石品位,使一部分非经济储量资源化。实现这一目标的前提之一是如何实现预选抛尾,使得在降低采出矿石品位,扩大资源储量的同时,不降低选矿的入选品位,不提高选矿的生产成本。因此无论是超贫磁铁矿石还是超贫氧化铁矿石,必须在入磨前采用高效的破碎、选别设备,寻求更好的抛尾效果,大幅度提高入磨原矿品位,采用更彻底的“多碎少磨”方法提升超贫铁矿石的选矿经济效益。
1 干式预选抛尾技术
对品位较低的贫磁铁矿而言,国内外大部分磁铁矿选矿厂均采用粗粒干式磁选抛尾的方法,在原矿入磨前抛弃大量尾矿来达到提高处理量、提高入选品位及降低生产成本的目的。但对于品位20.00%以下的超贫磁铁矿矿石而言,由于品位极低(其边界品位一般是人为圈定的),在矿石与围岩之间的品位差别很小时,干式磁选机的分选效果均不理想。例如马钢高村铁矿属露天采场,废石混入率低(3%左右),多次干选试验结果表明,抛尾产率10%~15%,品位提高不足2个百分点,尾矿中磁性铁损失大于1.5个百分点;昆钢大红山浅部熔岩干式磁选试验结果表明,抛尾产率13%,品位提高也不足2个百分点,效果不明显。前苏联卡奇卡纳尔采选公司选矿厂的超贫磁铁矿矿石品位为15.80%,粒度为10~25mm的破碎产品经干式磁选,抛尾产率仅4.00%左右,品位提高到17.50%左右。另外,研究和生产实践证明,由于受干式磁选设备分选原理的限制,即使将未来入选的超贫磁铁矿矿石在较细的粒度下采用干式磁选抛尾,也不能彻底解决入选品位过低、尾矿量大、选别成本高、经济效益低的难题,并且尾矿中磁性铁损失较大。因此在入磨前采用超细碎-湿式磁选抛尾技术是将来超贫磁铁矿预选抛废技术的发展方向。
2 磨矿、选别工艺
因为超贫、表外铁矿石的品位极低、铁矿物嵌布粒度很细,为达到节能降耗和提高精矿质量之目的,其磨矿、选别工艺一般采用多段阶段磨矿、阶段选别的原则流程。磁铁矿的选别工艺以弱磁选-细筛为主,如需进一步提高磁选精矿的品质,可采用弱磁选-反浮选联合工艺。在浮选药剂方面,虽然适合于鞍山式石英型铁矿石的反浮选药剂已取得重大进展,但是适合于其它类型铁矿石的高效反浮选药剂仍很少或者空白。
为了及早抛出大量尾矿,同时尽可能保证不损失有用铁矿物,相关铁矿石选矿厂基本上都从磨矿、选别工艺技术方面进行优化研究。国外倾向于棒磨-球磨的磨矿方案,例如前苏联卡奇卡纳尔采选公司选矿厂采用三段阶段磨矿(棒磨-球磨-球磨)、6次弱磁选的工艺流程。其中棒磨用于在粗磨粒度下(-0.076mm占20%左右)采用磁选抛弃大量尾矿,对于棒磨、磁选粗精矿再通过两段球磨、5次弱磁选后获得最终精矿,最终磨矿细度为-0.076mm占95%。而国内已生产的相关铁矿石选矿厂基本上都采用球磨-球磨的磨矿方案,即用球磨作为粗磨、磁选抛尾的磨矿设备,其磨矿成本高于棒磨。虽然采用磨矿、湿式磁选工艺技术能够达到提前抛弃大量粗粒尾矿之目的,但是还是不能彻底解决选矿能耗高、成本高的根本问题。
3 粗粒湿式磁选技术
目前国内选矿厂的常规破碎系统已能把一段入磨的矿石粒度降到-12mm以下,甚至-8mm。据初步统计,当磁铁矿矿石粒度破碎到10mm左右时,其中已有10%~30%的脉石矿物已经解离,可作为合格尾矿抛除。如能及时而有效地抛除这部分脉石矿物,不仅可提高球磨机的入磨品位、增大磨机的处理能力,达到节能、降耗、增效的目的,而且抛除的部分粗粒脉石不用进入尾矿库,因而还可大大延长尾矿库的服务年限。与此同时,磨矿设备也向大型化方向发展。这些有利条件为粗粒湿式磁选技术的研究、推广应用奠定了基础。中钢集团马鞍山矿山研究院研发出高效粗粒湿式磁选机专利产品(用于磨前抛尾)。该设备的主要技术性能指标:
(1)处理物料粒度0~20mm;
(2)设备处理能力80~200t/h;
(3)抛尾产率>15%;
(4)磁性铁损失≤1%;
(6)筒体、槽体使用周期≥1a。
该设备的关键技术是在常规湿式磁选机存在的粗粒磁选效果差、筒体易磨损、槽体阻塞以及精矿浓度低等缺陷问题方面,取得了突破性进展。通过磁系结构改进、筒体加入耐磨材料形成复合材料筒体、设计新颖的分选槽体结构、强制无冲洗水排矿设施等措施,以解决常规湿式磁选机存在的上述问题。某超贫铁矿石干式与湿式磁选抛尾对比试验结果表明,粗粒湿式磁选的抛尾效果明显优于干式磁选。
4 高效辊压超细碎技术
由于磨矿的能耗占整个碎磨作业的80%以上,因此“多碎少磨”技术一直是国内外极为关注的焦点之一,其中辊压技术是目前被公认的最先进的高新破碎技术。高效辊压技术是1984年由德国研制出来的高新破碎技术,已成功地应用于世界较多工厂,主要是水泥和石灰石工厂。近年来,在国外辊压机开始用于铁矿选矿厂,如美国EmpireIronOreMine用于破碎自磨机顽石,毛里塔尼亚SNIM/Zouerat用于破碎粗粒20~0mm铁矿石,智利某铁矿选矿厂用于破碎63.5~0mm铁矿石,而在国内尚处于研发或引进消化阶段。该设备具有单位破碎能耗低、破碎产品粒度细而均匀、占地面积少、设备作业率高和磨损件工作寿命长的特点,因此高效辊压技术是将来“多碎少磨”技术的发展趋势,是超贫、表外铁矿石得以高效综合利用的关键技术。
受马钢南山矿业公司委托,中钢集团马鞍山矿山研究院、德国洪堡公司对马钢南山矿低品位难选表外矿进行了前期的试验研究工作,对该矿石进行了辊压机半工业试验及选别工艺小型试验研究。结果表明,细碎产品经辊压机闭路时单位能耗为1.40~1.55kW/t,达到高效节能的效果,闭路筛分筛下产品的粒度分布为-1.4mm占80%、-315μm占50%、-71μm占30%。
根据辊面磨损试验结果,辊面工作寿命可达10000h。对高压辊压机产品小型试验研究表明,充分打散后用湿法磁选抛尾,可以将入磨原矿品位由20.00%左右提高到42.64%,提前抛弃产率占47.80%、品位8.31%的粗粒尾矿,提前抛尾效果十分显著。对于3~0mm左右的尾矿可以用分级方法分出部分粗粒,用于建筑用砂或堆存,可以大幅度降低尾矿输送量,经济效益和环境效益明显。
目前南山矿在工业实践引入高效辊压技术处理低品位混合矿石,初步调试结果显示该技术节能减排效果显著,对铁矿石破碎效果较好,使凹山选矿厂处理量由500万t/a提高至700万t/a,为该技术的推广应用奠定了重要基础。
建议与对策
(1)针对不同性质的超贫铁矿资源,为保证资源利用率、经济效益与环境效益最大化,在开发利用之前必须开展合理工艺流程优化研究,并进行综合技术经济分析,确定合理的入选品位和产品方案。
(2)通过引进、消化吸收和集成创新,加强辊压超细碎技术与粗粒湿式磁选技术的研发和推广应用工作,以真正实现超贫铁矿资源高效化利用及节能减排的理念。
(4)为减少粗粒尾矿的堆存量和细粒尾矿的输送排放量,减轻尾矿对环境的影响,应加强尾矿综合利用新技术的研究和应用工作。