传递系数(反映传递过程阻力大小的系数)

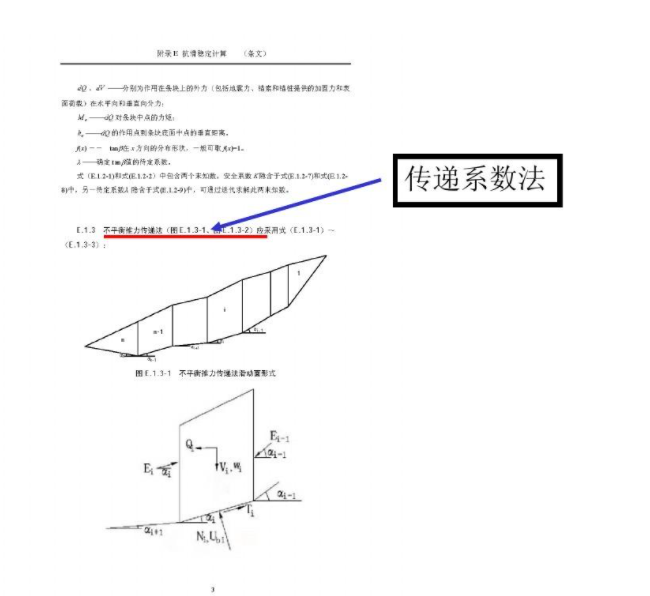
对于一端固定的杠杆,当可动端A转动时,固定端B也产生一定的弯矩,相当于近端的弯矩按一定的比例传到了远端,所以将固定端B弯矩与可动端A弯矩的比值称为由可动端向固定端的传递系数,用CAB表示,即:CAB=MBA/MAB或MBA=CABMAB。MAB为端A的劲度系数。
而对于化学反应过程中会伴随着物质和能量的变化,这就会产生能量和物质的传递过程,在计算时会用到传质系数和传热系数,他们统称为传递系数,影响传递系数的因素有很多。
传递系数
transmittance
chuán dì xì shù
传质系数和传热系数
CAB=MBA/MAB或MBA= CABMAB。
化学计算、能量传递计算
传递过程阻力的大小
颗粒几何形状、尺寸、反应条件等
简介
传递系数反映了传递过程阻力的大小,实质上也就是围绕催化剂颗粒外表面上层流边界层的厚薄。温度差和浓度差产生于层流边界层的两侧。处理实际的浓度也做均一的假定。这实质上是假定层流边界层的厚度处处相等,这样的假设将相间传递问题作为一维问题来处理,使复杂的问题大为简化而又保持足够的近似。
传递阻力的大小对于传递速率的影响至关重要,阻力越大则传递系数越小。流体与固体颗粒间的传质系数与颗粒的几何形状及尺寸、流体力学条件以及流体的物理性质有关。影响流体与颗粒间传热系数的因素同样是这些。
计算
海洋热通量的主要确定方法可大体分为涡动法、体积块法和剩余法3种。涡动法是利用边界层理论来分析海冰生消过程中冰水间的动量、热量和盐度的耦合过程,从而确定出海水对冰盖的热量传递;体积块法主要是根据冰点和海水的温差对海洋热通量进行直接计算;剩余法则是通过海冰下表面处的热量平衡来确定海洋热通量口。在海冰数值模拟,尤其是海冰数值预报中,体积块法应用最方便,它可以通过对水温、流速的预测来对海洋热通量直接计算。用体积块法计算海洋热通量的关键是对其中热传递系数的确定,而不同研究者所确定的热传递系数有很大的差异。
在对海洋热通量的研究中,人们建立了几种不同的体积块计算方法。但大多数考虑了冰水间温差、相对冰速以及海水定压比热容等因素,采用如下计算式:
式中:
为计算上式中的热传递系数,首先要确定海洋热通量。根据能量平衡原理,海洋热通量可由冰盖底面的相变潜热与冰内热传导的差值确定,对于薄冰还应考虑太阳辐射的影响,即:
式中:
分类
对于多相催化反应过程的第一步是反应物向催化剂颗粒外表面传递,这一步骤的速率可用下式表示:
式中,
由于化学反应进行时总量伴随着一定的热效应(放热或吸热),因而在反应物向催化剂颗粒外表面传递的同时,必然产生流体与颗粒外表面间的热量传递,进行放热反应时,热量从催化剂外表面向流体主体传递,吸热反应则相反,此传热速率可用下式表示:
式中,
式1~式3为相间传递的基本方程。上述两个传递方程都包含传递系数,即传质系数
由传热和传质的类比关系可知,用j因子的办法来关联气固传质和传热实验数据最为合适。传质j因子
式中
无论
上式应用范围为
应用范围为
根据传热与传质的类比原理有:
对比式4和式5可知,对于固定床,
由
实际生产中,在条件允许的前提下,力求用较大的质量速率以提高设备的生产强度,故属于外扩散控制的气固催化反应过程不多。硝酸生产中的铂网催化剂上的氨氧化反应属于外扩散控制,造成此种情况的原因有二:一是反应温度高达
影响因素
经过长期的探索和对生产实践进行总结。发现影响传递系数
式中
K——罐体垂直方向的空气直线速度(m/h);
·
S);K——经验常数
(一)搅拌功率的影响
1.搅拌的作用①使发酵罐内的温度和营养物质浓度达到均一,使组成发酵液的三相系统充分混合;②把引入发酵液中的空气分散成小气泡,增加了气一液问的传质面积,提高
2.影响搅拌功率的因素当流体处于湍流状态时,单位体积发酵液所消耗的搅拌功率才能作为衡量搅拌程度的可靠指标。实验测得公式6中的指数α的值为
式中d——搅拌器直径(m);
n——搅拌器转速(
ρ——发酵液密度(
P——搅拌功率(kW);
K——经验常数,随搅拌器形式而改变,一般由实验测定。
公式7在不通气和具有全挡板条件下的搅拌功率计算式,当发酵液通入空气后,由于气泡的作用降低了发酵液的密度和表观黏度,所以通气情况下的搅拌功率仅为不通气时所消耗功率的
3.搅拌功率对
(二)空气流速的影响
从式6看出,
(三)泡沫的影响
在发酵过程中,由于通气和搅拌的作用引起发酵液出现泡沫。在黏稠的发酵液中形成的流态泡沫比较难以消除,影响气体的交换和传递。如果搅拌叶轮处于泡沫的包围之中,也会影响气体与液体的充分混合,降低氧的传递速率。
(四)空气分布器形式和发酵罐结构的影响
在需氧发酵中,除了搅拌可以将空气分散成小气泡外,还可用鼓泡器来分散空气,提高通气效率。试验表明,当空气流量增加到一定值时,有无鼓泡器对空气的混合效果无明显的影响。此时,空气流量较大,造成发酵液的翻动和相流,对空气起到了很好的分散作用。鼓泡器只是在空气流速较低的时候对空气起到起的分散作用。此外,发酵罐的结构,特别是发酵罐的高与直径的比值,对氧的吸收和传递有较大的影响。