工件坐标系(编程时使用的坐标系)

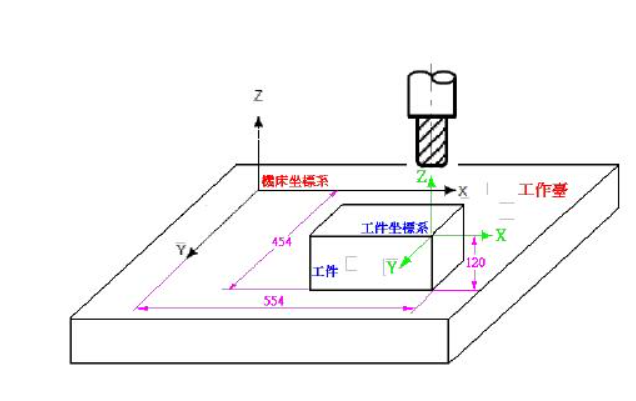
工件坐标系是编程时使用的坐标系,又称编程坐标系,该坐标系是人为设定的。建立工件坐标系是数控车床加工前的必不可少的一步。不同的系统,其方法各不相同。
工件坐标系
编程坐标系
通过试切对刀法
接触式传感对刀仪对刀法
建立方法
通过试切对刀法
建立工件坐标系(以在右端面建立工件坐标系为例)采用的是坐标系偏移转换的原理。它的操作原理是通过刀具对工件右端外圆和端面的试切削,及对所切外圆直径Φ的测量,将图示刀具试切后所在位置在工件坐标系中的预设坐标值,通过机床操作面板手动输入到数控车床相应的刀具补偿单元中,数控系统根据此位置预设的坐标值,经过坐标转换计算,确定工件坐标系原点的位置,从而将机床坐标系原点O机床偏移到所需的工件坐标系原点,这样就建立了一个以O为原点的工件坐标系。建立工件坐标系前,机床控制面板所显示的坐标是刀具当前位置在机床坐标系中的坐标:X坐标为Φx机床,Z坐标为ZA。建立了工件坐标系后,机床控制面板所显示的坐标即是刀具当前位置在工件坐标系中的坐标:X坐标为Φx工件,Z坐标为0。
在运行程序自动加工时,在程序开始首先要运行建立工件坐标系指令。机床数控系统不同,其建立工件坐标系的指令也不同,在FANUC数控系统中,常用T0101指令建立工件坐标系,G50指令也是建立工件坐标系指令,但由于其指令应用格式的局限,现多已不用。
接触式传感对刀仪对刀法
接触式传感对刀仪主要由触头和传感检测装置组成。用接触式传感对刀仪对刀的方法如图1-3所示,它是将刀具的刀尖接触到对刀仪韵周定触头,传感检测装置经过检测和坐标转换计算,自动将结果存入数控系统相应的单元中,从而建立工件坐标系,并同时设定刀具位置补偿值。用对刀仪对刀操作后,操作者方可使用该刀具进行加工。用接触式传感对刀仪对刀,其对刀精度高,加工效率也高,且容易操作。
应用实例
一。工件坐标系的设定
工件坐标系可以用下列指令设定:
G50X(α)Z(β)
式中α、β----------刀尖距工件坐标系原点的距离。
用G50X(α)Z(β)指令所建立的坐标系,是一个以工件原点为坐标系原点,确定刀具(一般指刀尖)当前位置的一个工件坐标系。工件坐标系一旦建立便一直有效,直到被新的所取代。为提高加工效率和保证加工精度,工件坐标系原点根据需要选在工件上任何一点都可以。该指令在执行时不产生运动,这是许多初学者较难掌握的地方。
二。操作步骤
1.试切对刀
对刀是数控车削加工中极其重要并十分棘手的一项基础工作,试切对刀法因其较高的准确性和可靠性而得到广泛应用。试切对刀过程中,巧妙建立工件坐标系能收到事半功倍的效果。现运用G50试切对刀的方法综述如下:
a、装夹好用于对刀的铝材工件和刀具;
b、主轴正转,手轮方式,基准刀沿表面A切削,将工件右端面车一刀;
c、Z轴不动,沿X轴释放刀具,停主轴;
d、取工件左端面中心为工件原点,测量A表面与工件原点之间的距离β,程序录入方式下,输入G50Z“β”,把当前Z向绝对坐标设为β,按刀补键,在相应的刀具参数偏置号处输入Z“β”;
e、手轮方式沿表面B切削;
f、X轴不动,沿Z轴释放刀具,停主轴;
g、测量距离α,程序录入方式下,输入G50X“α”,把当前X向绝对坐标设为α,按刀补键,在相应刀具参数偏置号处输入X“α”;
上述操作实际上是将用于试切的刀具作为标准刀,根据标准刀具建立坐标系,使其刀补为零刀架上的其他刀具则要通过和标准刀作比较,比较他们X和Z方向的长度之差,系统会自动计算出其差值作为其他刀具的刀补值。
2.找程序原点
程序原点为开始加工时刀尖的起始点及加工过程中的换切点,该点由编程确定。工件坐标系设定后,CRT屏幕上显示的是车刀刀尖相对于工件原点的坐标值,那么如何使刀尖在自动加工前处于程序原点“待命”呢?
例如要加工某工件,工件原点设在工件右端面中心,编程时程序原点指定为G50X100Z50,加工中确定程序原点的过程如下:
a、对刀后,装夹好工件毛坯;
b、主轴正转,手轮方式,基准刀平工件右端面A;
c、Z轴不动,沿X轴释放刀具至C点,输入G50X0Z0,电脑记忆该点;
d、程序录入方式,输入G01W-8F50,将工件车削出一台阶;
e、手轮方式。将刀具移至安全位置,停主轴,测量车削出的台阶直径α;
f、主轴正转,手轮方式下将刀尖返回C点;
g、程序录入方式,输入G50X“α”Z0,电脑将C点坐标根据工件原点正确设置并记忆,输入G00X100Z50,刀具运行至编程指定的程序原点,再输入G50X100Z50,电脑记忆程序原点。
在上述确定程序原点的过程中,步骤C巧妙利用G50设定中间桥梁C点坐标。因为G50执行时不产生运动,以内次该点坐标的具体数值并不重要,目的是让电脑记忆该点,方便测量台阶直径后正确返回。
3.中途断电后重新建立坐标系
数控车削加工中难免遇到突然停电的情况,当机床在断电状态时系统会失去对工件坐标值的记忆。解决方法如下:
a、接通电源,测量工件某处直径α;
b、启动主轴,用基准刀刀尖轻轻接触该处表面,输入G50X“α”;
c、退出刀具,停主轴,测量工件某处台阶至工件原点的距离Z“β”;
d、启动主轴,用基准刀刀尖轻轻接触该处台阶,输入G50Z“β”,再用G00指令运行至编程时指定的程序原点,用G50重新设置该坐标;
e、编辑方式下将光标移至能安全加工又不影响工件加工进程的程序段,按自动运行方式继续加工。
中途停电后,巧妙建立坐标系重新找回程序原点,既保证了加工精度,又不致重复全部加工操作过程,取得了很好的应用效果。
4.保证工件尺寸精度
数控车削加工中,有时会因各种原因不能保证工件尺寸精度。如装夹、找正、测量不当、操作者粗心找错程序原点、刀具磨损等都有可能产生废品,其中操作者粗心找错程序原点是可以通过重新建立工件坐标系解决的。例如加工某工件,停车检查时,我们发现工件尺寸精度颇有规律,所有外圆尺寸均比名义尺寸大60μm,发生这种情况的原因很可能是找程序原点是不慎找得不正确,偏离实际程序原点60μm。为了不致报废工件,办法是:暂停、复位、程序回零,在程序录入方式下,输入U—0.06,再将G50坐标设置为编程指定的程序原点坐标,重新运行加工,简捷地挽救了一个濒临报废的工件。